All distributors agree: cost optimization is the key to success. To meet the expectations of some of our clients, we have developed a strategic solution to reduce inspection costs while maintaining rigorous quality control: the Self Inspection Program (SIP). Let’s break down the advantages and steps of this program.
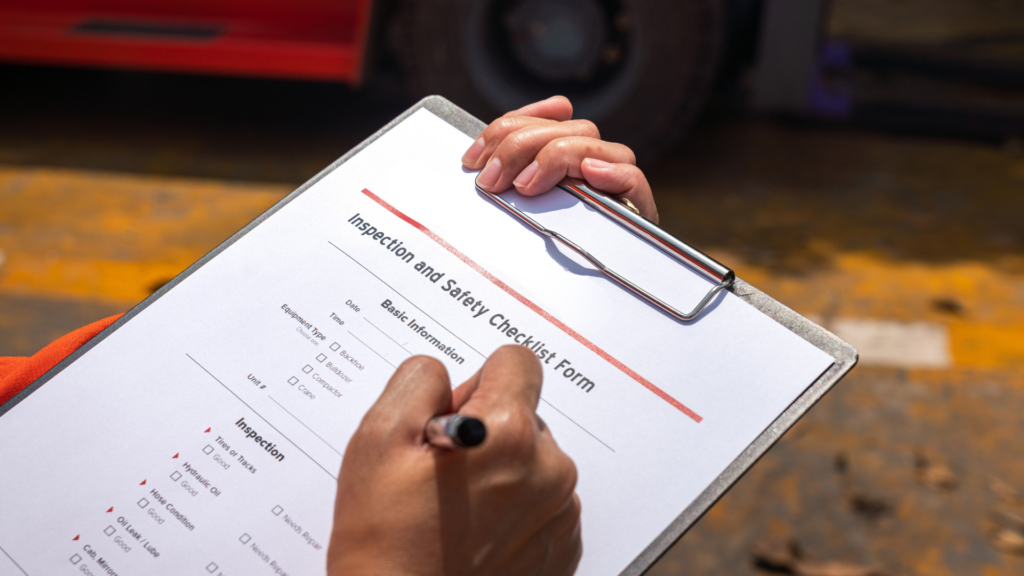
1. What is the Self Inspection Programme (SIP)?
The Self Inspection Program (SIP) allows selected and trained suppliers to carry out certain inspections and checks themselves under the supervision of EASTWISE, without knowing in advance whether or not we will intervene directly. This random and periodic approach guarantees compliance and data reliability. Each inspection follows our methods and tools, ensuring an optimal level of quality. The result: greater flexibility, increased supplier accountability and reduced costs for our customers.
The self-inspection program is a structured process in which only selected and trained suppliers carry out quality checks according to standards defined by Eastwise, while reporting their results. We conduct random and periodic visits to ensure compliance and data reliability.
As Jay, our Director of Operations and Quality, emphasises:
“SIP is an innovative and cost-effective solution that combines cost control with quality requirements. It ensures rigorous and predictive control without compromising surveillance. Since its implementation, quality has remained stable, while offering suppliers greater autonomy as their performance improves.
2. How does the SIP work?
Step 1: Supplier selection and training
Our quality control experts identify suppliers who are suitable to join the programme based on rigorous criteria:
- The maturity level of their quality system
- Their compliance history
- The complexity of the manufactured products.
Selected suppliers undergo specific training to ensure compliance with EASTWISE standards. This training includes modules on best quality control practices, deviation management, and the use of digital tools for traceability.
Step 2: Collaboration Between Suppliers and EASTWISE Quality Team
Inspections are conducted following strict protocols in direct collaboration with our experts. We use digital solutions for real-time monitoring, including the analysis of photos and videos of supplier inspections. EASTWISE ensures strict supervision and tracking at every stage of the process.
Step 3: Validation and Submission of Inspection Reports
Inspection reports are reviewed by our teams before being sent to our clients for final validation, ensuring total control over the quality and compliance of delivered products. With detailed reporting and regularly updated performance indicators, we guarantee optimal transparency throughout the process.
3. Three levers to optimise your inspection costs
Flexible Inspection Scheduling
Until just a few days before the end of production, the factory does not know whether the inspection will be conducted on-site or remotely. This uncertainty encourages suppliers to maintain a high level of rigor throughout the production process, avoiding last-minute preparations just for the inspection. This approach ensures greater adaptability to production constraints, optimizes resources, and motivates suppliers to maintain high-quality standards at all times.
Continuous and Transparent Reporting
Despite a reduced frequency of on-site visits, Eastwise remains actively involved in the control process and provides detailed reports. This ensures continuous monitoring and documentation of production quality.
Reduced Inspector Travel Costs
Reducing the number of on-site inspections eliminates part of the travel costs for inspectors, which can result in significant savings if suppliers demonstrate sufficient maturity. Additionally, it lowers the carbon footprint by reducing travel.
4. Why Choose SIP with EASTWISE?
Choosing SIP with Eastwise means opting for optimized quality control without compromising rigor. Thanks to this approach, our clients achieve a significant reduction in inspection costs while maintaining high standards. The integration of digital solutions also enhances traceability and responsiveness to potential quality deviations.
Fewer on-site inspections mean more flexibility, better responsiveness, and lower travel expenses, all while meeting production challenges.
At EASTWISE, we ensure strict oversight and complete transparency: every inspection report is validated by our teams before being sent to our clients.
Do you want to challenge your inspection process and optimize your costs without compromising quality?
Last updated on April 28th, 2025